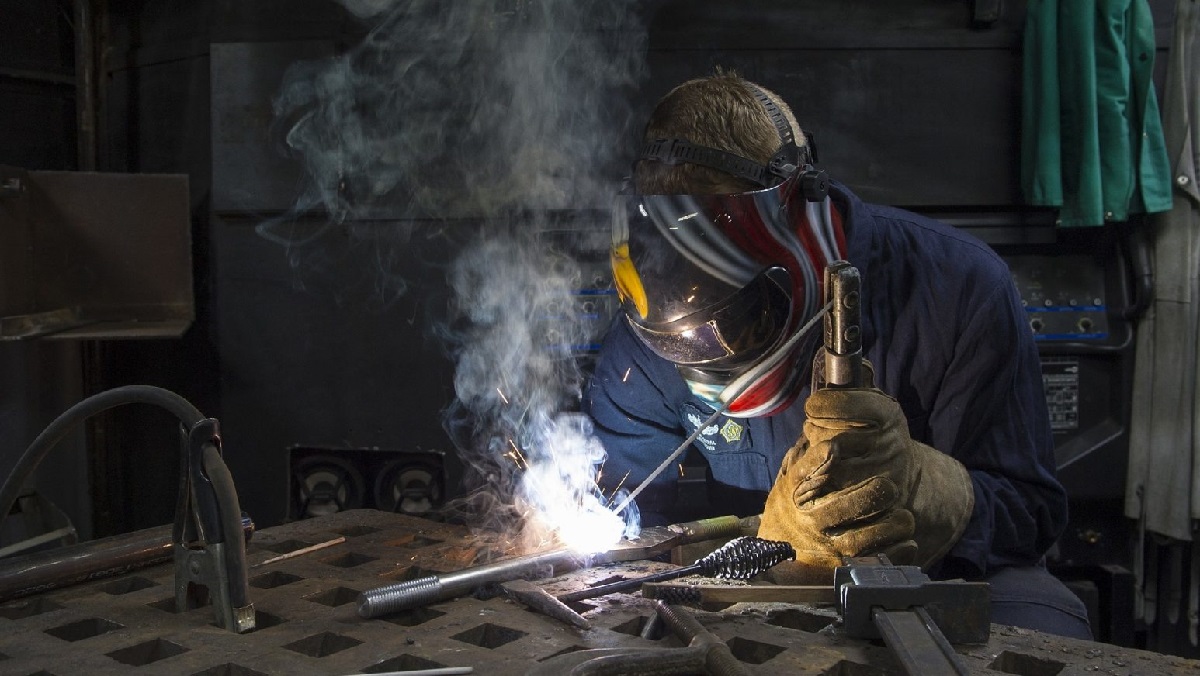
No metal filler is appropriate for any work. The chemical and mechanical properties, including its base material, the appropriate welding location, the equipment available, or the welding operator's skill set, among several other aspects, all factors involved in making the right selection possible.
When you're trying to maximize efficiency by higher deposition speeds, flow-core wires are always a viable choice.
These wires are renowned for their excellent performance and welding efficiency in businesses ranging from general production and manufacturing to mining, offshore, and shipbuilding. Flux-core wires have unique welding properties and conditions, benefits, and disadvantages. Getting to know flux-cored wires will help you decide if they are the correct decision.
Flux-Cored Wire Types
E71T-1
E71T-1 wires give unsurpassed efficiency for semi-automatic out-of-position welding. Its quick-freezing rutile slag offers the fastest vertical deposition rate, up to 7 pounds per hour, surpassed by some other semi-automatic arc welding operations.
Besides, the E71T-1 wires often give an incredibly smooth welding arc and limited spatter, and 100% carbon dioxide protecting steam. Argon/carbon dioxide mixtures are only used for the cleanest arc and better out-of-position efficiency. These are the justifications why E71T-1 has been the most common flux-core wire in the world. It is a top option for shipbuilding, structural steel, including general steel production applications.
E71T-8
E71T-8 wires give the best deposition speeds for semi-automatic out-of-position welding without shielding oxygen. The Lincoln Electric NRĀ®-232 will carry 4.5 lbs./hr. In the proper place, 50 percent quicker than the other E71T-8 wires. As this wire remains self-shielded, it is commonly used extensively and in field construction of steel beams.
E70T-4
For semi-automatic welding in a flat location, the E70T-4 is the best way to join a thick steel plate. It provides the fastest levels of semi-automatic disposal, up to 40 pounds every hour. This wire is commonly used for joining thick steels then there is no need for Charpy impact strength. This wire is often self-shielded, making it simple to use outdoors.
E70T-1
The tremendous rate of deposition of the gas-shielded flux-core wire is E70T-1. Compared to E70T-4, they provide slightly lower deposition speeds of up to 30 pounds each hour but provide better welding arc and Charpy impact strength properties. It offers better deposition speeds than GMAW, treats dirtier plates, and uses a lower cost of 100 percent carbon dioxide shielding coal. E70T-1s are commonly employed in structural steel production shops.
E71T-14
E71T-14 is the wire of choice for the welding of painted and galvanized sheet steel. The E71T-14 self-shielded wire contains core materials that burst in the arc, volatilize the steel layer, reduce cracking and porosity. The effect is better performing welding and quicker welding rates. E71T-14 wires are commonly used within the automobile industry for the production of galvanized steel.